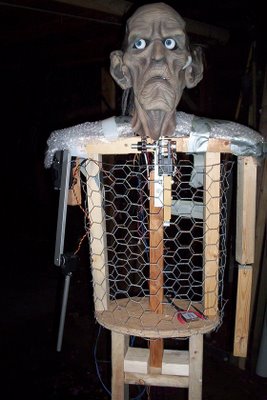
Later on a friend and I put together some special effects for another friend's Halloween party, and I must have made ten chicken wire/duct tape dummies. It works but your hands wind up looking like you tried to pick up a feral cat with your bare hands!
Using chicken wire/duct tape shells closes in your design, making it very difficult to get back inside the animatronic when something breaks or needs adjustment. I even tried using cut up pieces from old 2 liter water containers, but the problem was still that this techinque limited or eliminated the ability to easily get back inside the animatronic.
Salvation came from an unexpected source. I email regularly with my friend Stan in Ontario, Canada, and he turned me on to a material known as "Wonderflex".
A quote taken directly off of the internet:
Wonderflex looks like a piece of plastic, but it becomes soft and malleable when heated. It can be shaped by hand or over a mold while hot. Once it cools down it hardens retaining the shape. It can be re-heated and reshaped as many times as necessary, or worked in sections. It glues to itself if enough pressure is applied. It can be cut with scissors and finished with paint, gluing fabric on top, or any other method. It can be heated with a heat gun, a microwave oven, or dipped in hot water.
This stuff sounded too good to be true, so I ordered some. This stuff is great!
I purchase Wonderflex from Dazian Fabrics, but only because I get next day delivery via UPS Ground. Google Wonderflex and you can find it from many sources.
The product comes in 39" X 57" sheets .035" thick. I bought a mannequin off of Ebay and got into the sheet molding business:

Cutting a piece to fit, I got out my industrial heat gun and went to it. As the Wonderflex gets hot, it gets very flexible, and very easy to drape over a form and press into place, because the Wonderflex gets so hot heavy duty gloves are used to smooth the product into place and smooth out any wrinkles.

Once the skin has been hand molded onto your form, it's just a matter of using a utility knife to cut various parts off of your mold.

Here I've cut off the chest/stomach part and bolted it to an aluminum strip.

Attached to Clod's wooden frame, the Wonderflex skin is a marvelous replacement for chicken wire/duct tape shells.
On another project I combined the Wonderflex skin idea with an aluminum frame, producing a very light weight but sturdy design:

Using aluminum frame elements eliminated the dead weight of using a wood frame, and making the aluminum support struts was fairly straight forward.

Since this project was a ghoul rising about ten feet in the air, weight was an important consideration. Using the Wonderflex/aluminum frame concept, I was able to design a "ghoul" that weighed less than 25 pounds.

Here is a photo of the ghoul's framework while the lift mechanism is being tested. As you can see the framework is pretty much empty space, and certainly allows getting "back inside" the animatronic if something needs to be tightened, fixed, etc.
No comments:
Post a Comment